What is Pulse Laser Clean?
Time:
2024-10-12
Author:
Wendy
Data source:

Pulse laser cleaning is an advanced surface treatment process that utilizes high-intensity laser pulses to remove contaminants from a substrate without the use of chemicals or abrasives. This non-contact method employs a focused laser beam directed at the workpiece, which rapidly increases the energy absorption and temperature of either the substrate or surface pollutants. The resulting thermal effects lead to the efficient removal of unwanted materials.
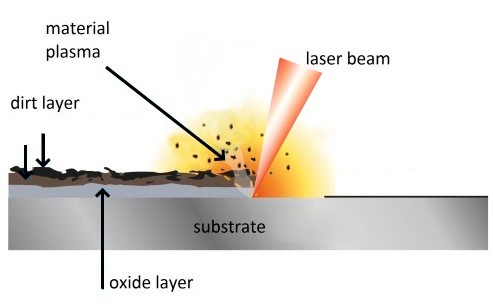
The process operates through two primary mechanisms:
- Selective vaporization: When surface contaminants absorb the laser energy preferentially, they undergo rapid thermal expansion and vaporization. This sudden change in volume creates localized stress, causing the pollutants to separate from the substrate with minimal impact on the base material.
- Laser-induced shock waves: In cases where the substrate absorbs more laser energy than the contaminants, it experiences rapid thermal expansion. This generates mechanical shock waves that propagate through the material, effectively dislodging surface pollutants through a process known as laser spallation.
The effectiveness of pulse laser cleaning depends on careful optimization of laser parameters, including wavelength, pulse duration, energy density, and repetition rate. These factors are tailored to the specific substrate material and contaminant properties, ensuring efficient cleaning while minimizing the risk of substrate damage.
This technique offers several advantages over traditional cleaning methods, including:
- Precision: Allows for selective removal of contaminants with micrometer-level accuracy
- Environmental friendliness: Eliminates the need for chemical solvents or abrasive media
- Versatility: Suitable for a wide range of materials and contaminants
- Automation potential: Easily integrated into production lines for high-throughput processing
Pulse laser cleaning has found applications in various industries, including automotive manufacturing, electronics, cultural heritage preservation, and aerospace component maintenance.
Practical application
Laser cleaning is a versatile technique that can effectively remove both organic and inorganic contaminants, such as metal corrosion, metal particles, dust, etc. The following are some practical applications of this technology, which has already reached a high level of maturity and is widely used.
Mold cleaning:
Every year, tire manufacturers around the globe produce hundreds of millions of tires. During the production process, the cleaning of tire molds must be efficient and effective to minimize downtime.
Traditional cleaning methods, such as sandblasting, ultrasonic cleaning, or carbon dioxide cleaning, require the mold to cool for several hours before being transported to the cleaning equipment. This process takes a significant amount of time and can easily compromise the accuracy of the mold. Additionally, the use of chemical solvents and the resulting noise can raise concerns over safety and environmental protection.
The laser cleaning method offers a solution to these challenges. As the laser can be transmitted through optical fiber, it has great flexibility in use. Additionally, the laser cleaning method can be combined with optical fiber to direct the light to hard-to-reach areas of the mold, making it easier to clean. Furthermore, the laser cleaning process does not gasify the rubber, eliminating the risk of toxic gas emissions and ensuring a safe working environment.
The laser cleaning technology for tire molds has been widely adopted in the European and American tire industries.
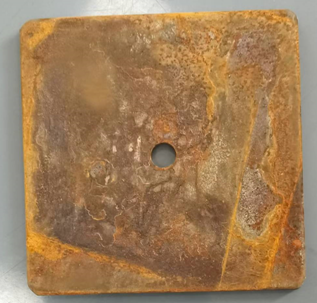
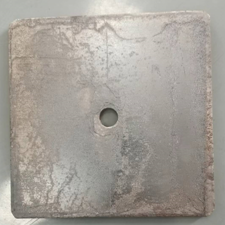
Cleaning of weapons and equipment:
Laser cleaning technology is widely utilized in the maintenance of weapons.
The laser cleaning system is an efficient and quick way of removing rust and contaminants, and it also allows for selective removal, resulting in an automated cleaning process.
Compared to chemical cleaning, laser cleaning not only provides a higher level of cleanliness, but also minimizes surface damage to the objects being cleaned.
Removal of old aircraft paint:
In Europe, laser cleaning systems have been widely used in the aviation industry for a long time.
Aircraft surfaces need to be repainted after a certain period, but before this can happen, the old paint must be completely removed.
Cleaning of building exterior wall:
With the rapid growth of China’s economy, more and more skyscrapers are being built, and the challenge of cleaning their exterior walls is becoming increasingly prevalent. The Laser cleaning system provides an effective solution for cleaning building exterior walls through optical fibers that are up to 70 meters in length.
This system can effectively clean all types of pollutants from various surfaces such as stone, metal, and glass, resulting in a cleaning efficiency that is several times higher than conventional cleaning methods.
Cleaning in the electronic industry
The electronic industry utilizes laser technology for oxide removal. Precision decontamination is crucial in this industry, making laser oxide removal an ideal solution.
Before welding a circuit board, it is necessary to completely remove any oxides from the component pins to ensure optimal electrical contact. This process must not damage the pins.
Laser cleaning is able to meet these requirements and is highly efficient. In fact, a single pin only needs to be exposed to the laser once for effective decontamination.
Precision degreasing cleaning in precision machinery industry:
In the precision machinery industry, it is often necessary to remove esters and mineral oils used for lubrication and corrosion resistance from parts. This is typically done through chemical methods, but chemical cleaning often leaves residues.
Laser deesterification is an alternative that can completely remove esters and mineral oils without damaging the surface of the parts. This is achieved through the use of a shock wave.
The shock wave is formed by the explosive gasification of the thin oxide layer on the surface of the parts, leading to the removal of pollutants rather than through mechanical interaction.
Pipeline cleaning in the reactor of nuclear power plant:
The laser cleaning system is also utilized in the cleaning of pipes in nuclear power plant reactors.
By using optical fibers, a high-power laser beam is introduced into the reactor to directly remove radioactive dust, resulting in easy-to-clean materials. Additionally, remote operation ensures the safety of personnel.
In conclusion, laser cleaning plays a crucial role in many fields, including automobile manufacturing, semiconductor wafer cleaning, precision parts processing and manufacturing, military equipment cleaning, building exterior wall cleaning, cultural artifact protection, circuit board cleaning, precision parts processing and manufacturing, LCD cleaning, chewing gum residue removal, and many more.
key word:
pulse laser clean,laser clean,metal clean,molds clean,pipe clean
Next page:
Next page:
RELATED NEWS
2024-11-12